WHEEL SPECIFICATIONS
Construction: 3-Piece Lightweight Beadlock
Weight Reduction: Pocketing / Undercuts / Billet Forged Beadlock Ring / ARP Hardware
Pricing Starts: $4350 per wheel
OPTIONAL FEATURES:
– Titanium Hardware
3-PIECE CONSTRUCTION
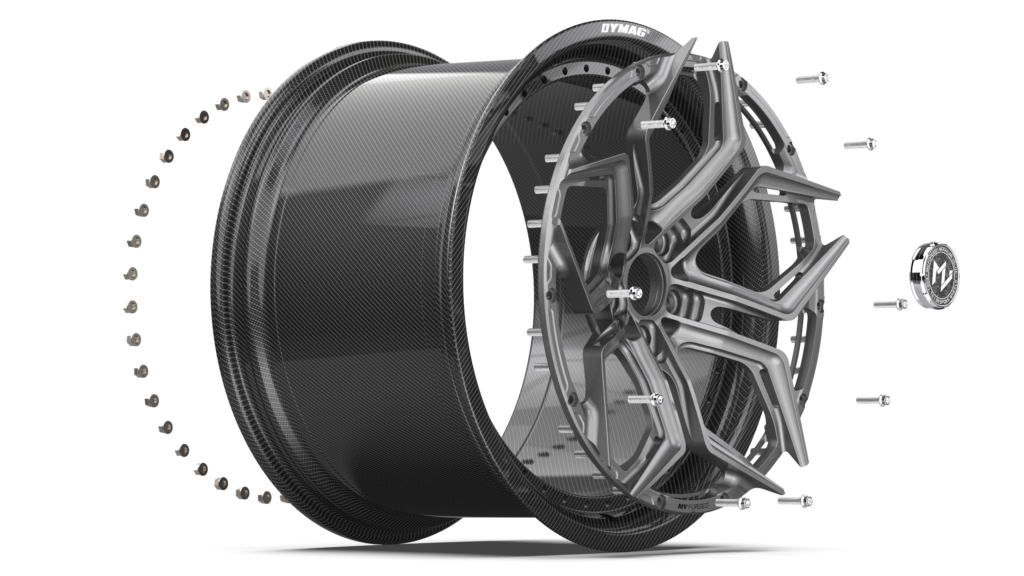

MR-208CL DYMAG | DETAILS
VIEW FINISHES
◤VIEW FINISHESWHEEL GALLERY
◤VIEW WHEEL GALLERYView our wheel gallery to view the latest finishes, techniques and behind the scenes footage.
VEHICLE GALLERY
◤VIEW VEHICLE GALLERYView our vehicle gallery and get inspired showcasing our latest collaborations, designs, and vehicles.
DESIGNED TO PERFORM.
At MV Forged, Performance and longevity is the hallmark of a great wheel. That is why we place a heavy emphasis on precision designing and expert craftsmanship. Aiming to achieve the highest quality wheels in its class.
THE FOUNDATION.
Each set of MV Forged wheels are meticulously designed, engineered, and crafted in our Southern California Facility. Our team at Modular Velge with over 70 years of combined forged wheel experience allows us to have full control over the quality of our process. Each order goes through Finite Element Analysis (FEA) testing to ensure the most optimal combination of lightweight, durability, and strength.
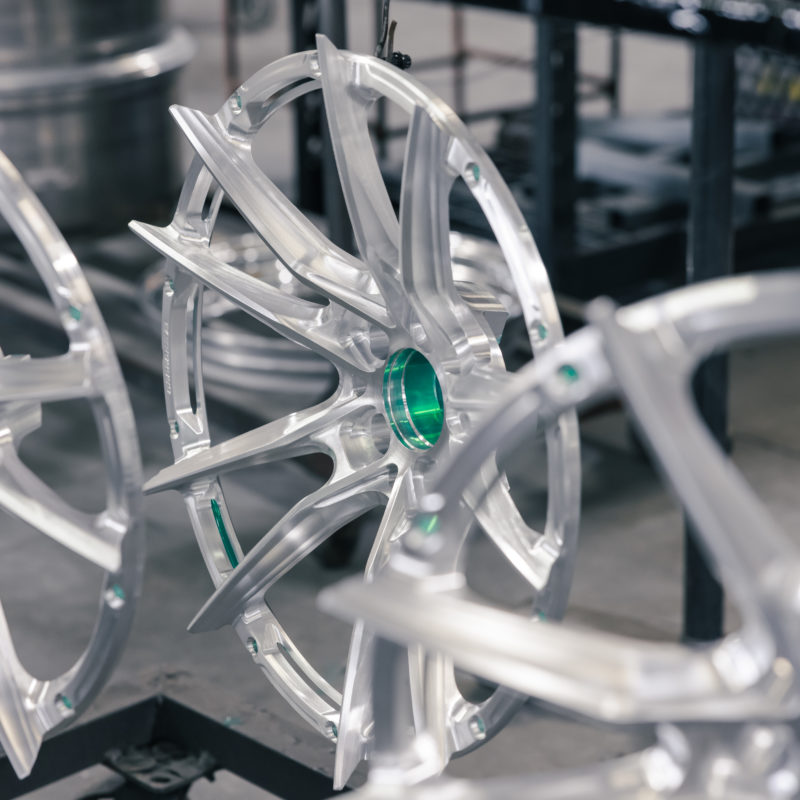
MILLING.
Once the profile is completed, the forgings are then turned over to the mill process. The mill process is where the design comes to life. As mill cycles run through a series of pre-selected tool sets and milling paths that can take up to 8 hours per wheel to achieve the utmost precision.
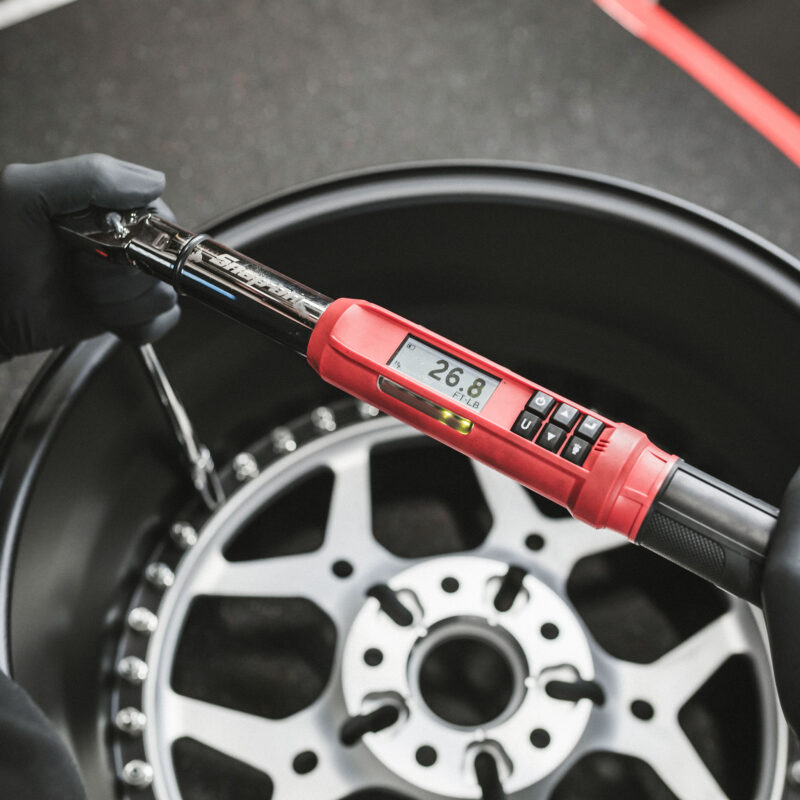
ASSEMBLY.
The assembly stage is one of the most critical stages in the manufacturing stage. First step is to check the run-out of every wheel to guarantee the wheels are balanced to eliminate vibrations and wobbling. We chose to use Digital Snap-On® Torque Wrenches vs generic torque wrenches. One of the advantages is that it can more precisely control the amount of torque that’s applied to a bolt without losing any torque capacity.